How Technology Is Enhancing Cross Bore Inspection
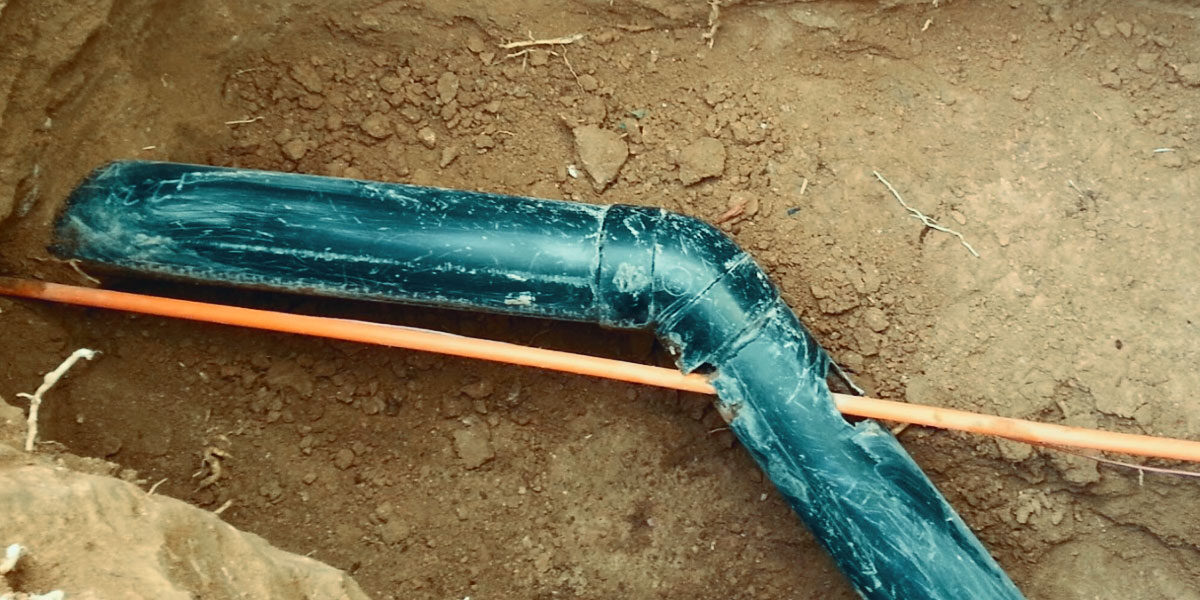
How Technology Is Enhancing Cross Bore Inspection
Cross bores are more common than you might initially think. According to the Cross Bore Safety Association (CBSA), underground sewer inspections show there's about one cross bore in every half-mile of mainline sewer. And when you consider the number of problems that cross bores can pose to properties and people, their presence—especially at this sort of frequency—can pose a significant problem.
Maintaining underground infrastructure safety is important—and inspecting for and addressing cross bore gas lines or cross bore electrical lines is a big part of ensuring safety. In this post, we'll discuss the importance of cross bore inspection, advanced technologies that are streamlining operations and improving safety, and more.
Importance of Core Bore Inspection
As you know, cross bores are underground utility lines (gas, electric, etc.) that were inadvertently installed through another utility line, typically via trenchless installation and often during land development. Cross bores often intersect with sewer or septic lines, posing problems during a backup. If such sewer or septic lines are cleared with mechanical devices, there's a chance that these tools will also damage the cross bore line. Should these cross bore utility lines be damaged, it could lead to electrocution or a gas leak into buildings, which could cause major property damage and bodily harm.
Another issue associated with an undetected cross bore is the structural weakening of the sewer pipe and the overall sewer system through which it is installed.
Conventional cross bore locating and inspection methods have their limitations. Poor data and record-keeping during the construction of "legacy projects" can make these cross bores difficult to locate. When they are found, they are often in areas that have not been properly maintained. Common issues with conventional cross bore inspections include collapsed lines and the inability to traverse the main sewer line. Furthermore, conventional horizontal drilling methods used outdated directional installation techniques, which add to the challenges of cross bore inspection.
Advanced Inspection Technologies
Preventing issues with cross bores begins with accurate identification of existing utility assets before new utility lines are installed or old ones are replaced. At National Underground Group, we employ advanced technologies to achieve this.
One of our key technologies is the industry-leading Robotic Lateral Launch System. These robotic visual inspection systems provide real-time CCTV images of mainline, lateral pipes and manholes. Equipped with an underground pipe camera and running on self-steering robotic crawlers, they offer 360-degree views, an unfolded view and a geometric view, giving operators a comprehensive understanding of subsurface pipe infrastructure.
The Robotic Lateral Launch System can inspect up to 1,000 feet of mainline in a single run, both with or against the flow. This data is easily offloaded to analysts, enhancing inspection efficiency and ensuring accuracy.
We also create a geographic information system (GIS)-based time-stamped library of events as inspections and cross bore projects progress. This system allows us and our clients easy access to data and inspection records, which can be viewed anytime and from any place, ensuring the safety of communities and infrastructure.
Enhancing Safety and Efficiency
Advanced technologies, such as underground pipe camera inspection, enhance safety and efficiency by significantly reducing cross bores and related risks. These technologies streamline the inspection process, reducing the time and resources needed for successful completion.
Additionally, these inspection tools provide property owners with detailed records and data on existing infrastructure before installing new utility lines. This proactive approach helps prevent common issues, offering peace of mind and reducing the risk of cross bores during future horizontal installations.
Comprehensive Data Management
Effective data management is crucial for tracking production, isolating cross bore inspections and time-stamping cleared locations. At National Underground Group, we build comprehensive data libraries for our clients using geographic information systems (GIS) to integrate and supply cross bore inspection information. These libraries provide actionable insights through our user-friendly online portal.
By accessing these data libraries, users can link inspection data to GIS-based mapping systems, easily isolate inspection details and assess a range of infrastructure and pipe types. This streamlines complex data management and enhances transparency.
Our cloud-based solutions further improve data accessibility and reliability. Clients can access the information anytime, anywhere, ensuring that inspection records are always up-to-date and easily retrievable. This technology supports informed decision-making and efficient management of underground infrastructure projects.
In conclusion, here are the key advantages of using advanced technology for cross bore inspection:
- Enhanced Accuracy: Advanced technologies provide precise identification of existing utility assets, reducing the risk of cross bores.
- Improved Safety: Real-time CCTV and comprehensive inspection systems enhance safety for communities and workers.
- Increased Efficiency: Streamlined inspection processes save time and resources, ensuring faster project completion.
- Comprehensive Data Management: GIS-based data libraries and cloud solutions offer easy access to inspection records, supporting informed decision-making.
- Proactive Prevention: Detailed records help prevent future issues by providing critical insights before new utility lines are installed.
Experience Enhanced Infrastructure Safety and Reduced Cross Bore-Related Risks
Contact us today for more information on our cross-bore underground pipe inspection services and the advanced technologies we administer to ensure the safety and reliability of your infrastructure.